By Dan Cassens, Prof. of Wood Products at Purdue University
February 19, 2020
Although local enforcement and rules differ in each part of the country regarding whether or not you need to have an official grade stamp on your lumber in order to use it for construction projects, we’ve found that many people don’t know how to go about doing it right in their area. Many err on the side of caution, not using lumber that they could be using, and others build whatever they want, however they want, hoping the inspector won’t notice. The right solution is knowing your local requirements. This article intends to give you an overview of how you can use your own lumber in permitted structures, and give you resources to take the next step to using and/or selling lumber that will meet your local requirements. We’re not talking about using your own lumber for trim, flooring, paneling, etc. The rules for lumber used in the actual structure of the home is what is important.
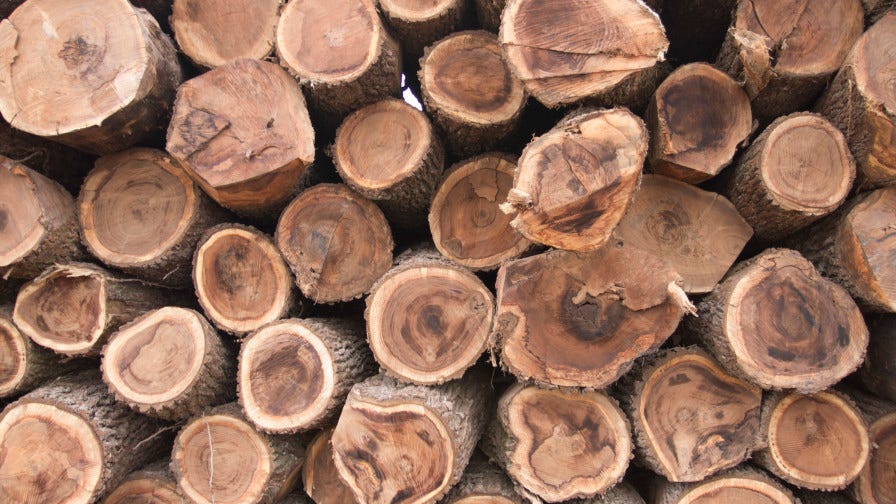
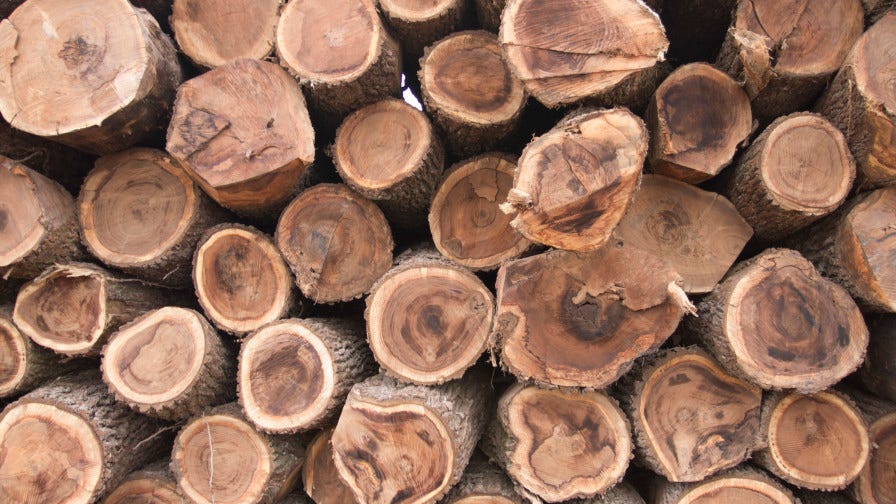
Five Steps to Using Your Own Lumber in Permitted Structures
Anyone contemplating producing lumber for construction should follow these steps before sawing.
1. Check with your local city, county, and/or state building code office to find out the exact requirements in your area. Requirements and the level of enforcement vary. Don’t be satisfied until you have seen the rules yourself. Keep a copy for future reference.
2. Purchase the softwood grading rules book that applies to the species of lumber you’ll be using. Thoroughly review the pertinent parts of the book to make sure you understand what the standards apply.
3. Once you have a written plan on how to proceed, contact the appropriate softwood lumber grading agency to discuss your plan with them and to make certain that your lumber will meet all of the requirements, such as thickness, widths, and lengths, moisture content, and required other items. Checking out all of the details before sawing can save time and wasted materials. (If going the self-certification route, make sure your certification is up-to-date)
4. Saw and dry your lumber according to your specific plan.
5. Schedule a visit with the lumber inspector, make sure you have enough time for his visit, and your area is properly laid out for inspection. Make certain any documentation is prepared and available should the inspector ask for it.
The Grade Stamp
As part of a structure, each piece of lumber carries a certain amount of load. Softwood grades for dimension and timbers have been established according to engineering methods that determine how much load each piece is capable of supporting. When a building is inspected, the inspector will look for a grade stamp on the lumber. This grade stamp is the only way for the inspector to determine if the lumber used in the structure is acceptable. The grade stamp is extremely important to building inspectors, as it is required by all building codes. The code is usually enforced at the county level, where a building permit is required before any construction can begin. The building can be rejected if the lumber is not grade stamped. The level of code enforcement can vary by county, however a lack of enforcement does not mean you can disregard building codes. Be certain to check with your county building inspector and permits office to determine exactly what is required. Past experiences may not predict future expectations. There may be some state and local exceptions when the lumber is produced and used for one’s own building projects.
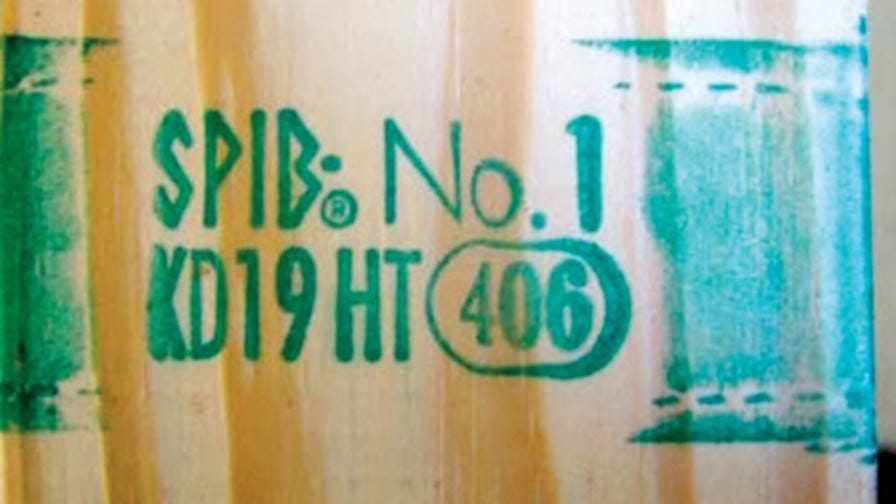
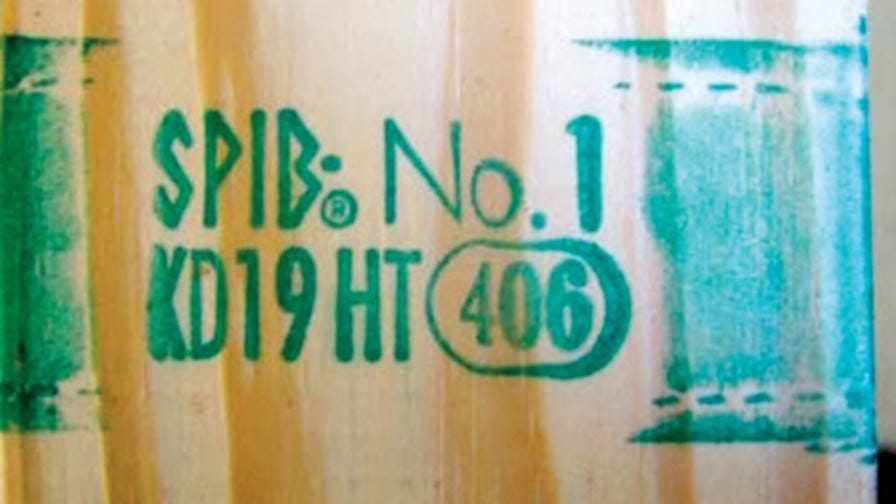
Example grade stamp above showing Southern Pine Inspection Bureau (SPIB) as the agency, the grade as No. 1, kiln-dried (KD) to 19 percent moisture content, heat treated (HT), and producing mill lumber 406. The species is not given but implied as SPIB deals exclusively with Southern Pine lumber.
Understanding the Softwood Grade Stamp
Grade stamps are used in the softwood industry as a means for the seller to provide the buyer, building inspector, or other interested parties with five pieces of important information. A softwood grade stamp provides several types of information required by the ALSC (American Lumber Standard Committee)
- Trademark - identity of agency quality supervision
- Mill identification - product manufacturer name, brand, or assigned mill number
- Grade designation - i.e. No. 2 or Stud Grade
- Species - individual species or combination
- Seasoning - moisture content classification at time of surfacing
- S-Dry - 19% maximum moisture content
- MC 15 - 15% maximum moisture content
- KD - kiln dried to moisture content indicated in grading rules
- S-GRN - over 19% moisture content (unseasoned)
- HT - heat treated
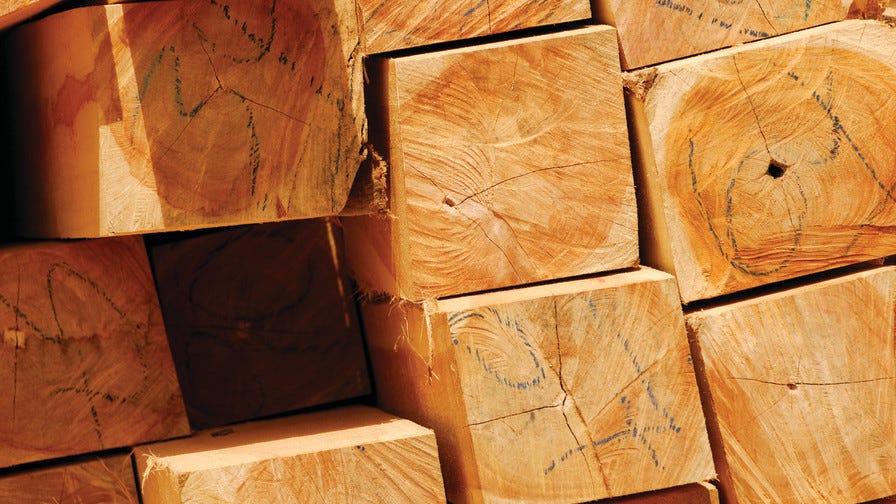
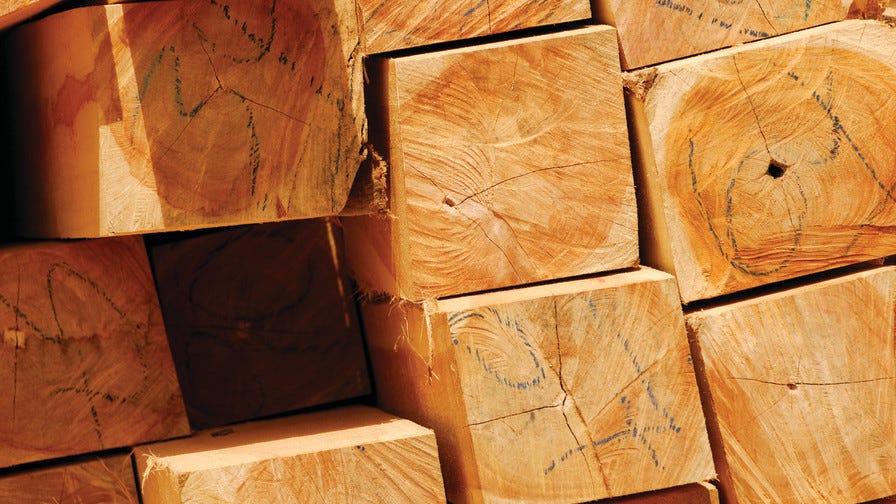
Getting Your Lumber Graded
Producers of small quantities of softwood or hardwood lumber to be used in construction can call for a “certificate inspection.” When a certificate inspection is requested, the grading agency will arrange for their first available or nearest inspector to travel to the location of the lumber. The lumber is grade-stamped, and a certificate is issued in regards to the inspection. The lumber is then eligible to be used in building construction. The owner of the lumber should be prepared to turn and move the boards for the inspector. Also, presorting the lumber by widths and lengths is important. Additional sorting by estimated grade will further speed up the process. The lumber may be rough or surfaced. Lumber having moisture content in excess of 19 percent will be marked “S-GRN.” Air-dried lumber or that with a moisture content of less than 19 percent will be stamped “S-DRY.” Sawyers should be certain that they follow the size requirements set forth by the rule writing agencies for different species. In order to finish to the sizes required, lumber must be cut oversized to allow for shrinkage during drying, planing, and sawing variation.
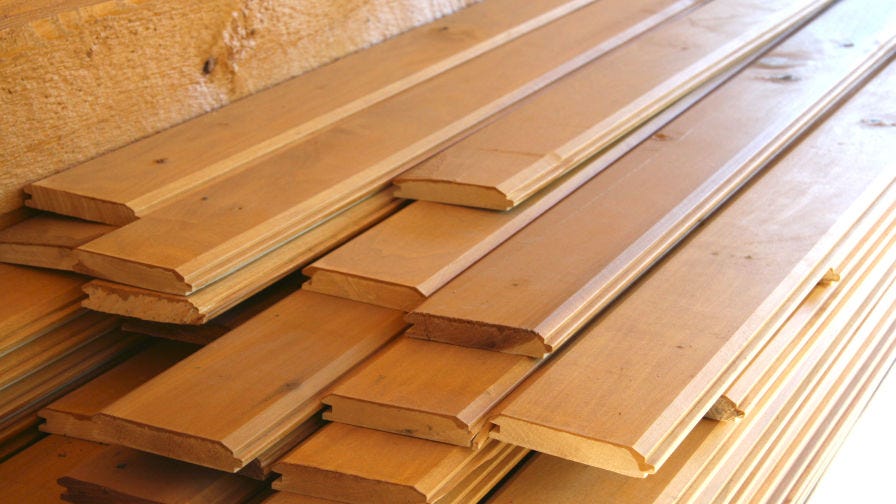
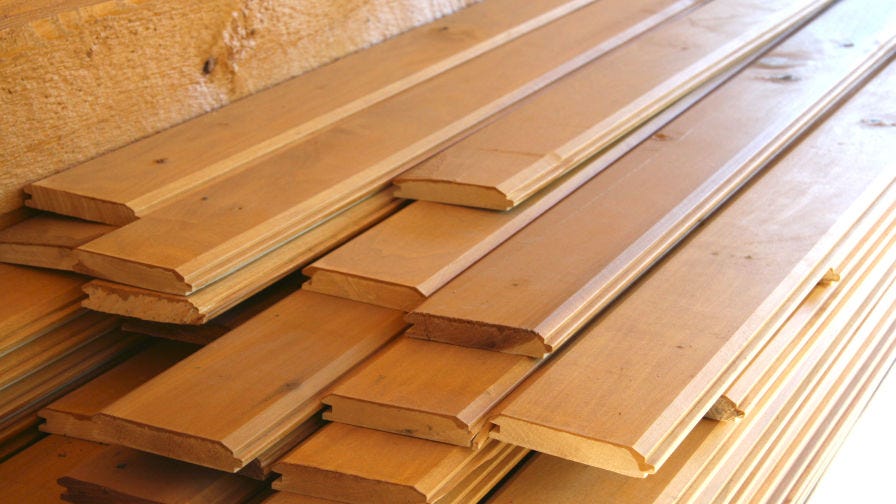
The Bottom Line
In most of North America, using your own lumber for construction material is an option available to you, and in some places, it is actually encouraged and rewarded. We hope that this short introduction to the topic has given you some good direction to finding out how to go about it in your own area. Rules can change, so ten years from now, when you pull out this article again to reference, the bottom line will still apply: Find out what your local requirements are, and abide by them!
Resources
For current rule writing and grading agency lists:
American Lumber Standard Committee
www.alsc.org
alsc@alsc.org
301.972.1700
Canadian Lumber Standards Accreditation Board
www.clsab.ca
info@clsab.ca
613.482.2480
About the Author: Dan Cassens is a professor of Forest Products in the Department of Forestry and Natural Resources at Purdue University in Lafayette, Indiana. In one way or another, he has been handling wood and or trees every day for the last 40 years. He attributes an increase in his knowledge about wood from operating his Wood-Mizer LT40 portable sawmill for nearly 20 years.
Although local enforcement and rules differ in each part of the country regarding whether or not you need to have an official grade stamp on your lumber in order to use it for construction projects, we’ve found that many people don’t know how to go about doing it right in their area. Many err on the side of caution, not using lumber that they could be using, and others build whatever they want, however they want, hoping the inspector won’t notice. The right solution is knowing your local requirements. This article intends to give you an overview of how you can use your own lumber in permitted structures, and give you resources to take the next step to using and/or selling lumber that will meet your local requirements. We’re not talking about using your own lumber for trim, flooring, paneling, etc. The rules for lumber used in the actual structure of the home is what is important.
Five Steps to Using Your Own Lumber in Permitted Structures
Anyone contemplating producing lumber for construction should follow these steps before sawing.
1. Check with your local city, county, and/or state building code office to find out the exact requirements in your area. Requirements and the level of enforcement vary. Don’t be satisfied until you have seen the rules yourself. Keep a copy for future reference.
2. Purchase the softwood grading rules book that applies to the species of lumber you’ll be using. Thoroughly review the pertinent parts of the book to make sure you understand what the standards apply.
3. Once you have a written plan on how to proceed, contact the appropriate softwood lumber grading agency to discuss your plan with them and to make certain that your lumber will meet all of the requirements, such as thickness, widths, and lengths, moisture content, and required other items. Checking out all of the details before sawing can save time and wasted materials. (If going the self-certification route, make sure your certification is up-to-date)
4. Saw and dry your lumber according to your specific plan.
5. Schedule a visit with the lumber inspector, make sure you have enough time for his visit, and your area is properly laid out for inspection. Make certain any documentation is prepared and available should the inspector ask for it.
The Grade Stamp
As part of a structure, each piece of lumber carries a certain amount of load. Softwood grades for dimension and timbers have been established according to engineering methods that determine how much load each piece is capable of supporting. When a building is inspected, the inspector will look for a grade stamp on the lumber. This grade stamp is the only way for the inspector to determine if the lumber used in the structure is acceptable. The grade stamp is extremely important to building inspectors, as it is required by all building codes. The code is usually enforced at the county level, where a building permit is required before any construction can begin. The building can be rejected if the lumber is not grade stamped. The level of code enforcement can vary by county, however a lack of enforcement does not mean you can disregard building codes. Be certain to check with your county building inspector and permits office to determine exactly what is required. Past experiences may not predict future expectations. There may be some state and local exceptions when the lumber is produced and used for one’s own building projects.
Example grade stamp above showing Southern Pine Inspection Bureau (SPIB) as the agency, the grade as No. 1, kiln-dried (KD) to 19 percent moisture content, heat treated (HT), and producing mill lumber 406. The species is not given but implied as SPIB deals exclusively with Southern Pine lumber.
Understanding the Softwood Grade Stamp
Grade stamps are used in the softwood industry as a means for the seller to provide the buyer, building inspector, or other interested parties with five pieces of important information. A softwood grade stamp provides several types of information required by the ALSC (American Lumber Standard Committee)
- Trademark - identity of agency quality supervision
- Mill identification - product manufacturer name, brand, or assigned mill number
- Grade designation - i.e. No. 2 or Stud Grade
- Species - individual species or combination
- Seasoning - moisture content classification at time of surfacing
- S-Dry - 19% maximum moisture content
- MC 15 - 15% maximum moisture content
- KD - kiln dried to moisture content indicated in grading rules
- S-GRN - over 19% moisture content (unseasoned)
- HT - heat treated
Getting Your Lumber Graded
Producers of small quantities of softwood or hardwood lumber to be used in construction can call for a “certificate inspection.” When a certificate inspection is requested, the grading agency will arrange for their first available or nearest inspector to travel to the location of the lumber. The lumber is grade-stamped, and a certificate is issued in regards to the inspection. The lumber is then eligible to be used in building construction. The owner of the lumber should be prepared to turn and move the boards for the inspector. Also, presorting the lumber by widths and lengths is important. Additional sorting by estimated grade will further speed up the process. The lumber may be rough or surfaced. Lumber having moisture content in excess of 19 percent will be marked “S-GRN.” Air-dried lumber or that with a moisture content of less than 19 percent will be stamped “S-DRY.” Sawyers should be certain that they follow the size requirements set forth by the rule writing agencies for different species. In order to finish to the sizes required, lumber must be cut oversized to allow for shrinkage during drying, planing, and sawing variation.
The Bottom Line
In most of North America, using your own lumber for construction material is an option available to you, and in some places, it is actually encouraged and rewarded. We hope that this short introduction to the topic has given you some good direction to finding out how to go about it in your own area. Rules can change, so ten years from now, when you pull out this article again to reference, the bottom line will still apply: Find out what your local requirements are, and abide by them!
Resources
For current rule writing and grading agency lists:
American Lumber Standard Committee
www.alsc.org
alsc@alsc.org
301.972.1700
Canadian Lumber Standards Accreditation Board
www.clsab.ca
info@clsab.ca
613.482.2480
About the Author: Dan Cassens is a professor of Forest Products in the Department of Forestry and Natural Resources at Purdue University in Lafayette, Indiana. In one way or another, he has been handling wood and or trees every day for the last 40 years. He attributes an increase in his knowledge about wood from operating his Wood-Mizer LT40 portable sawmill for nearly 20 years.